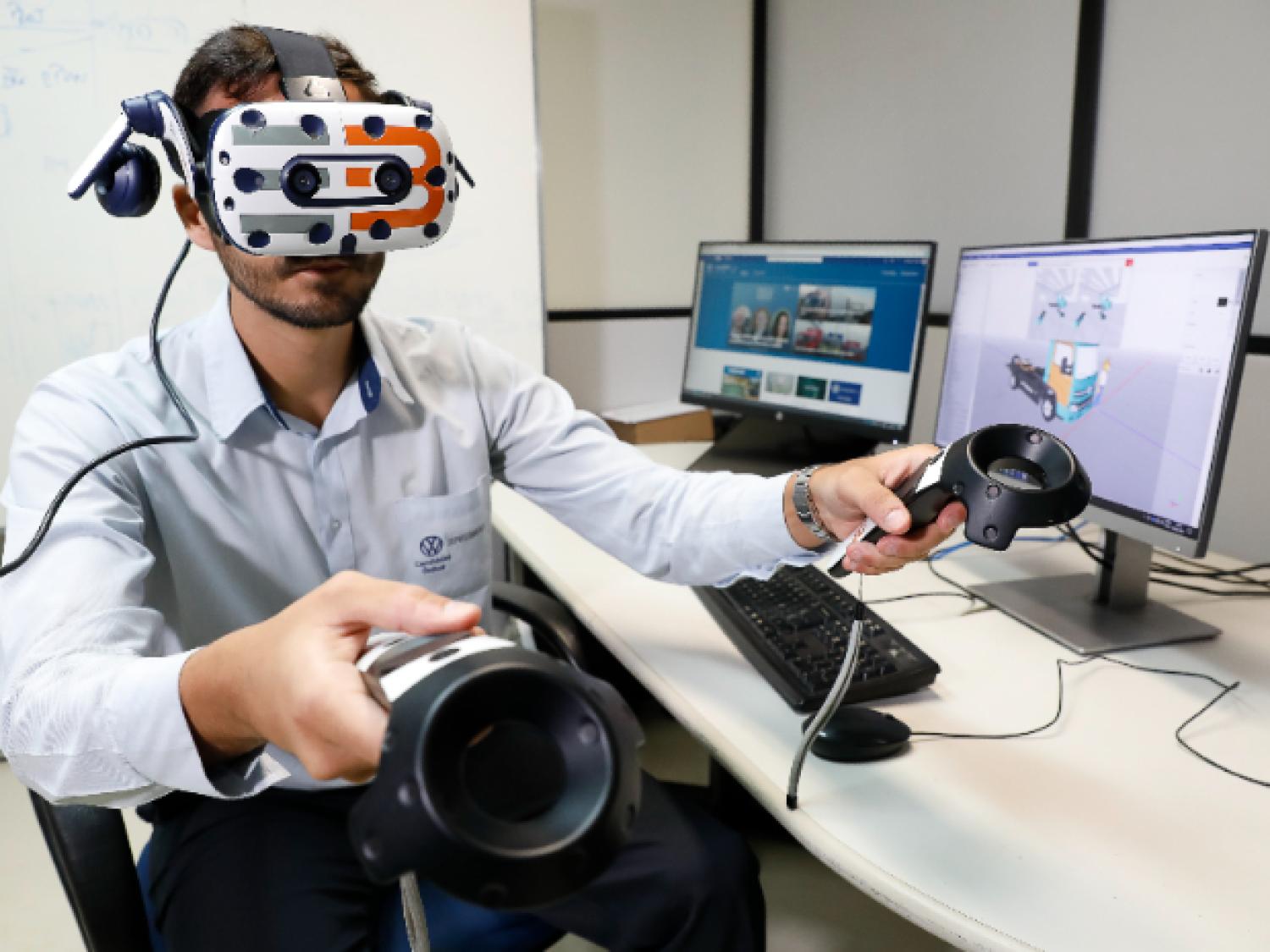
- Technology allows development processes to be completed at three times the speed and reduces additional project costs by 65%
- Assembler expects to invest a total of R$1 million in digital innovation throughout 2024
Technologies are continuing to be developed at a rapid pace at Volkswagen Truck & Bus, and virtual reality is gaining prominence as the assembler, which has established a global engineering center in Brazil, launches new products. VWTB has used virtual reality in manufacturing analyses since 2022. This important tool allows development processes to be completed up to three times faster and reduces project costs by 65%, in addition to guaranteeing increased safety and optimizing activities performed. The company expects to invest a total of R$1 million in digital innovation throughout 2024.
“Virtual reality tools have significantly impacted productivity and development costs since being implemented. By optimizing internal processes, we have doubled our capacity to produce virtual prototypes and are able to validate designs in a completely digital format. Taking product design and assembly simulation tests into consideration, progress made in the area of virtual reality allowed 25% of the approval phase to be moved forward and eliminated two to four physical vehicles per project, drastically reducing amounts disbursed, in addition to having a key environmental impact,” Luiz Salles, Manufacturing Manager at VW Truck & Bus, explained.
With software developed based on VWTB’s parameters, together with integrated 3D glasses and joystick, virtual reality is also fast becoming a powerful ally in boosting sustainability. When compared to the traditional prototyping process, having a digital alternative available optimizes the use of energy resources and reduces the consumption and disposal of resources such as metals, plastics, wood, and other materials.
360° Innovation
Volkswagen Truck & Bus’s development and production center in Resende (RJ) was recently renovated and now houses one of Latin America’s most modern truck production lines. VWTB’s manufacturing process is based on 4.0 concepts and makes use of advanced robotics and Big Data intelligence. In order to ensure increased productivity and operational safety, virtual reality to train production teams.
“Our assembly line is one of the most diverse of its kind in the global automotive industry and highly complex. Approximately 250 variations of vehicle models – for both trucks and buses – are sent through the same structure, and we need to ensure that the processes occur with an extremely high level of precision, synchronization, and fluidity. In addition to the remaining technologies mentioned and the experience offered by multidisciplinary teams, the use of virtual reality in our assembly line, which simulates final operations and exchanges with the operational team, allows us to make the necessary adjustments before models enter into production and correct failures before they have an impact on the final result,” Salles added.
VW Truck & Bus is inspired by the results obtained so far and plans to continue investing in plant technologies and digital processes, which will in turn take the company to new heights.