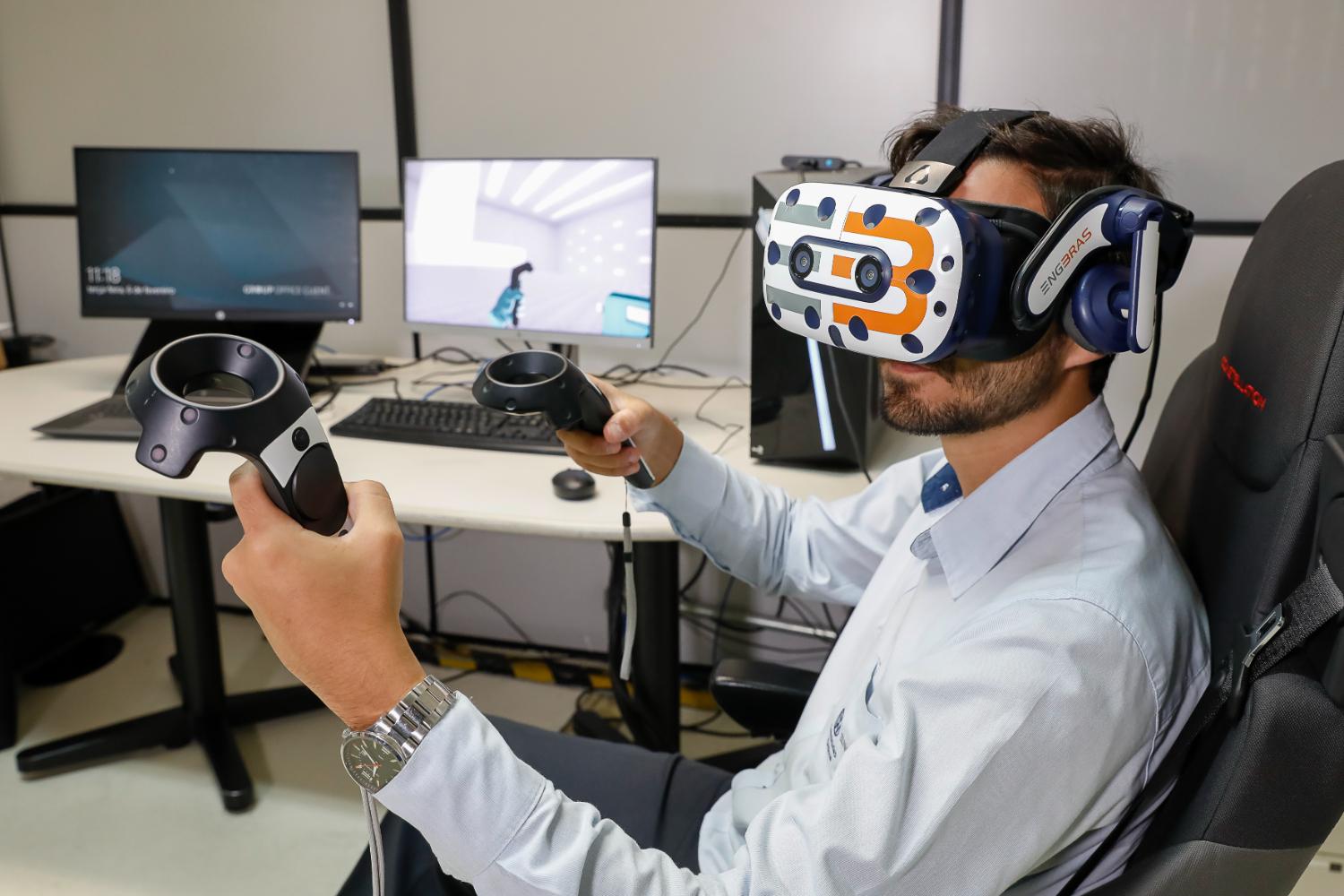
- Company invests in digital factory fronts, circular economy and collaborative spaces
- Monitoring system makes it possible to minimize stops by up to 87%
- Dialogue in collaborative spaces generates engagement for process improvement
- Circular economy project enables the recycling of 36 tons of plastic waste per year
Volkswagen Truck & Bus advances year by year by implementing innovative solutions that combine cutting-edge technology, strong commitment to the well-being of its employees and sustainable practices, a point that justifies the delivery of increasingly modern vehicles and its leading position in the market. Through strategic projects such as digitalization, circularity and focus on people management, the company redefines standards by optimizing processes, reducing costs and promoting an increasingly humanized work environment. Such measures have reflected positively on operational efficiency and products delivered to the market.
Present from the prototyping and development phases, digitization is also a powerful feature in the production process. The cloud system known as a supervisory system, with the ability to continuously monitor the main data from machines, equipment and processes, identifies faults, inefficiencies and deviations from the targets set based on information generated by more than 100 programmed logic controllers. This system significantly improves the quality of information, accelerating decision making and reducing downtime and maintenance production losses. In the paint pretreatment facility, for example, the supervisor made it possible to reduce downtime by up to 87%, increasing productivity and equipment availability at this stage of the process.
Access to real time information also allows staff to gain valuable insight into operational performance by identifying patterns, trends and opportunities for improvement. In the case of chassis and suspension production, intelligent monitoring enabled a 4% gain in the production balance.
Other factors have enhanced the company's results, such as investment in initiatives that promote the development and well-being of its employees. The transformation of the management islands on the production line into collaborative spaces has increasingly encouraged interaction and exchange between operators. In this way, knowledge sharing and the development of innovative solutions have increased significantly. In their most recent action, the talks on the islands resulted in 140 improvements implemented in a month.
Daily contact with those responsible for practical processes provides the company with new points of view on aspects related to quality, production, safety and employee engagement. From the information collected, assembly processes are improved, failures are corrected, improvements in workstations are delivered, and much more. In a survey carried out in August, the more than 1,000 employees involved indicated great satisfaction with the changes implemented.
Demonstrating a strong commitment to sustainability, the automaker also adopted a project to reuse clips, covers and other materials originally intended for disposal. The initiative makes it possible to recycle 36 tons of plastic waste a year and involves the participation of the line's operators. It has made a significant contribution to reducing waste, reducing environmental impact and promoting the concepts of circular economy and recycling among employees.
Changes in habits and a new way of looking at things are encouraging assemblers to take a leading role in the search for improvements and new sustainable initiatives. Thanks to familiarity with the processes, they become the main vehicles for the transformation of the company's routines. VWCO's trajectory demonstrates that the industry of the future will be marked by the convergence of technology, sustainability and people.